Logistics control tower with management capacity
Solution for the management of load/unload operations
Optimizes, automates and digitizes communications between agents to achieve significant savings in the logistics operations of a platform or plant.
Increase your productivity
We offer the best possible platform for managing loading and unloading operations. A product that provides a methodology that optimizes, automates and digitizes communications between agents to achieve significant savings in the logistics operations of a platform or plant.
This improves the productivity of the plants. Our vision is: to manage in the best possible way so that during the loading and unloading operation there are no waiting times, so that it occurs at an optimal time for all parties and in the best location. With this we ensure that the operation is as optimal and short as possible in addition to reducing the time dedicated to managing the agenda.
Get visibility
Hardman is also a control tower, so it offers advanced visibility solutions. You will be able to transfer information to the different agents that work with you: carriers, clients, other operators, suppliers, freight forwarders and others.
From monitoring the cold chain to forecasting delivery to the customer.
And document management: whether documents to your clients, documents from your suppliers, international documents generated by freight forwarders, health inspectors or any other agent that is involved in your routes.
Our systems ensure that everything goes on time and in proper order and only generate alarms when a deviation is detected that could put a load at risk.
What we fight against
What is the worst situation you face?
Need a product and not have stock
What is the worst stock out there?
Have a product and not need it
And we fight against…
What is the worst cost we have?
Pay to stand
Operates as a pit stop
The average waiting time at a logistics platform is 3 and a half hours. Even if you have a good indicator, it is very likely that it will not go below the hour.
This is not free, it is tremendously expensive. A platform that moves 100 trucks, this inefficiency translates into:
- More than 9,200 productive hours
- About 2,000,000 kilos of CO2
- And direct costs greater than €1,400,000
- 8,700 hours of own personnel doing low-value tasks
But these costs are only part, the tip of the iceberg, the costs are in the human resources necessary to manage all this.
Sign up! Check our potential
What to expect
Manage info
The time allocated to informing the different agents of the work that is related to our plants simply disappears.
Occupancy of slots
Slot occupancy should be >90%. That means fewer people stopped and resources more used. Once again, greater productivity.
Puntuality
The double commitment methodology causes the punctuality rate to naturally increase, as well as the reduction of no-shows.
Inability to load
The times in which due to the disk or others a load in the end is not carried out disappear. The cases are so extreme that they border on 0.
Waiting time
Drastic reduction in waiting times. Whatever waiting time you have, you can estimate that you will reach < 5 minutes
Recover time
From your team, of value, to do important tasks and not have to manage the day to day. This becomes managed autonomously.
Logistics control tower with management capacity
A union point for all the data related to your logistics chain. Access the real status of everything, at any time and from anywhere. Data updated in real time.
It digitizes all communication between the different agents: who and what should load or unload, when they will arrive, waiting times, dock management, check-in records, quality and much more.
Where it is, when it should arrive, temperature, humidity or any other factor that is decisive for your cargo.
All this data is managed and analyzed by our systems so that loads do not stand still. Our systems analyze to identify risks and possible incidents. Predict behaviors and situations that may become problems.
Your agents are informed about these risks, this way it is not necessary for them to dedicate themselves to managing the ordinary in search of risks. They only have to manage the extraordinary, the exception and recover valuable time for your business.
The control tower becomes your ally, an AI agent that constantly monitors that everything flows.
And the work does not end with supervision, it also provides valuable data, useful information for decision making.
Satisfaction
Keep your customers informed of where their expedition is, the conditions it is in and when it will arrive.
A well-informed customer, especially in adversity, is a well-cared-for customer. And taking care of customers is key to their satisfaction. And there is nothing better for a business than satisfied customers.
Incidents
We will inform you in real time of any problem or incident that occurs in your expeditions., In this way it will no longer be necessary to manage the ordinary to identify risks. These come to you, so you recover your time and you only have to manage the extraordinary: Exception management.
Artificial intelligence
Our systems identify risks, look for problems even before they occur, so you can get ahead of them.
An invaluable help in the form of an intelligent agent that reduces the ordinary workload of your work group and adds value to your product.
Improvement rate
Soluciones para
Carriers
Logistic operators
Productors or Manufacturers
Intermodal
Keys
AUTOMATION
All systems work with a single soul. We reinforce the information between them so that everyone follows the marked circuits. If a merchandise does not arrive correctly, we modify the invoice and issue it reflecting reality.
DIGITALIZATION
All aspects of freight transport are digitized. Expeditions, communications between agents, messages from the driver, delivery notes, incidents. Everything.
A central point of reliable information.
VISIBILITY
Throughout the supply chain. Even if there are subcontractors, even if it goes through 20 hands. We link the systems of all parties to give the best visibility. We even integrate drivers and their vehicles.
INTEGRATION
Our systems do not involve more work, a new platform to feed. It feeds on the others and provides them with new valuable data. We never require data that has been registered in another system, we integrate it.
MONITORING
Focus on what's important. We analyze data from all sources, avoiding the ordinary management. We look for potential incidents so that you act on them when there is still time to mitigate them.
CONFIDENCE
We offer you high-value tools to improve your processes. We are not interested in telling you where a certain merchandise is. You can notify the client to indicate that we are delayed. This is called building trust.
Sign up! Check our potential
Success stories
Never trust commercial messages. Here is a sample of what our clients say about us.
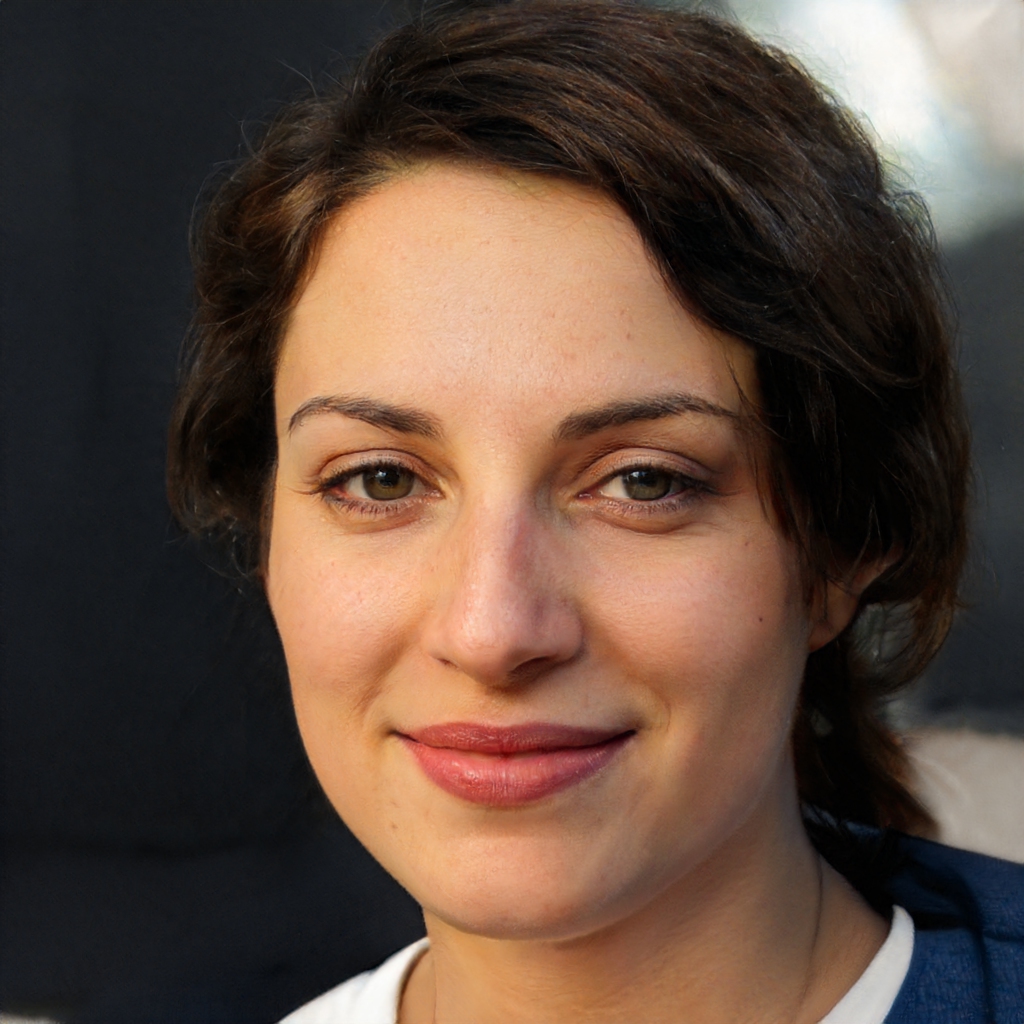
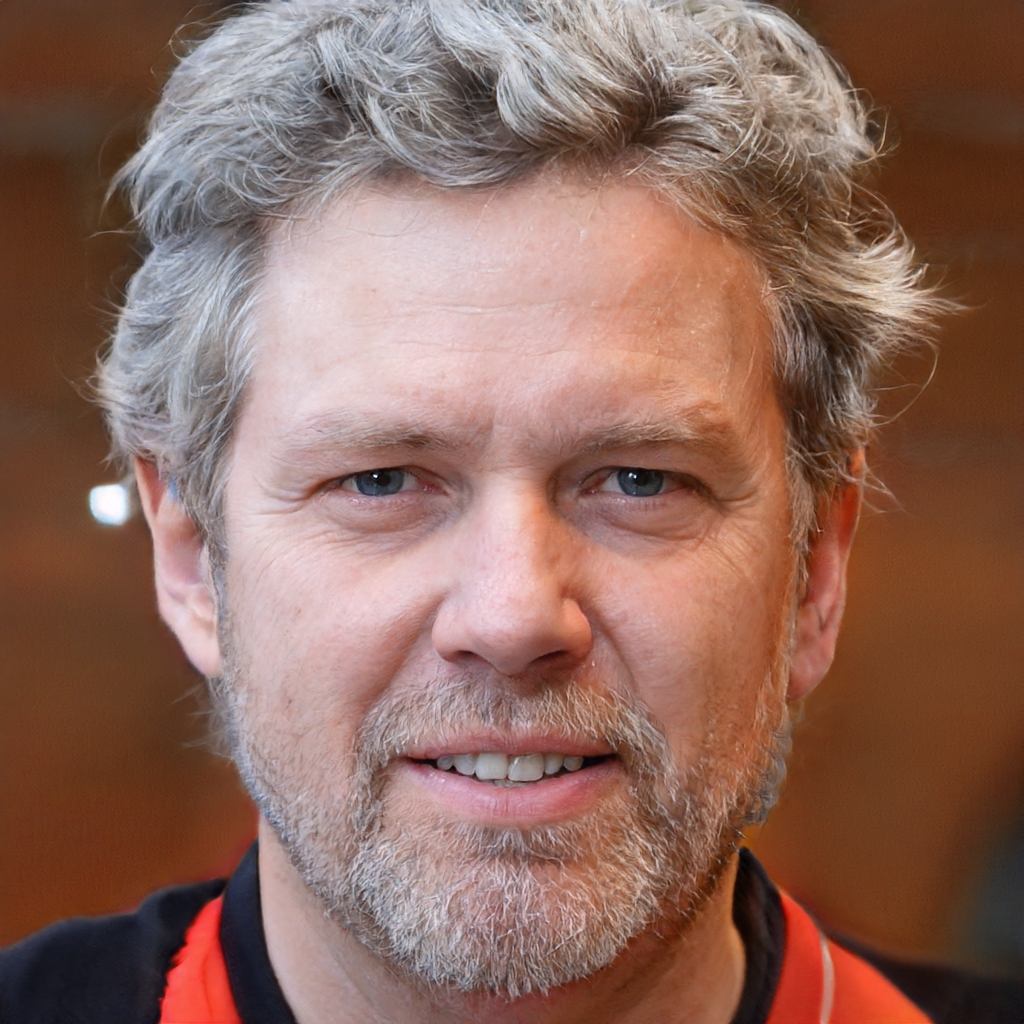
It was like putting on glasses. We now have a clear and trustworthy vision of all our expeditions: past, present and future. for We are proactively alerting you when there is a problem with a delivery.
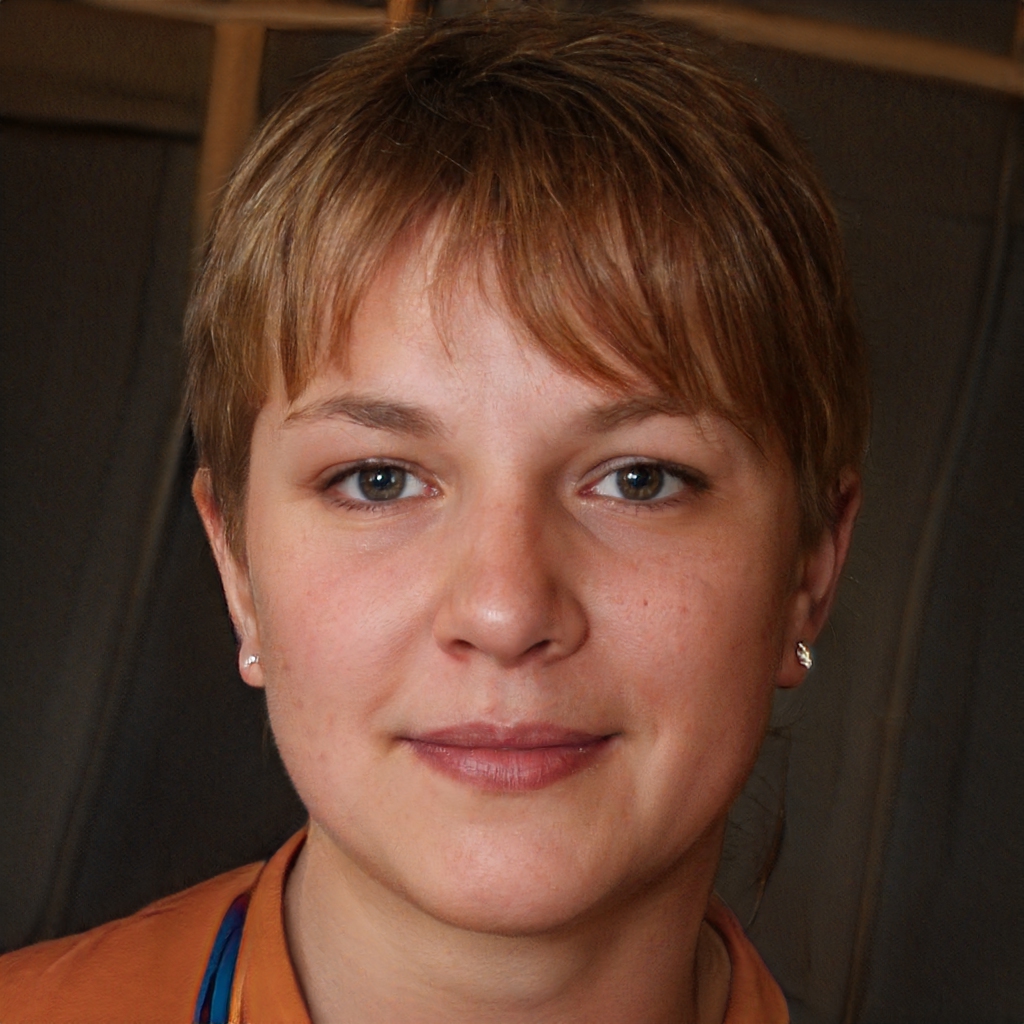
We have detected a big difference in the opinion that our clients have of us. for We have a good product but we lost control as soon as it was loaded onto the truck, now we respond even before delivering it. for We have detected a big difference in the opinion that our clients have of us.
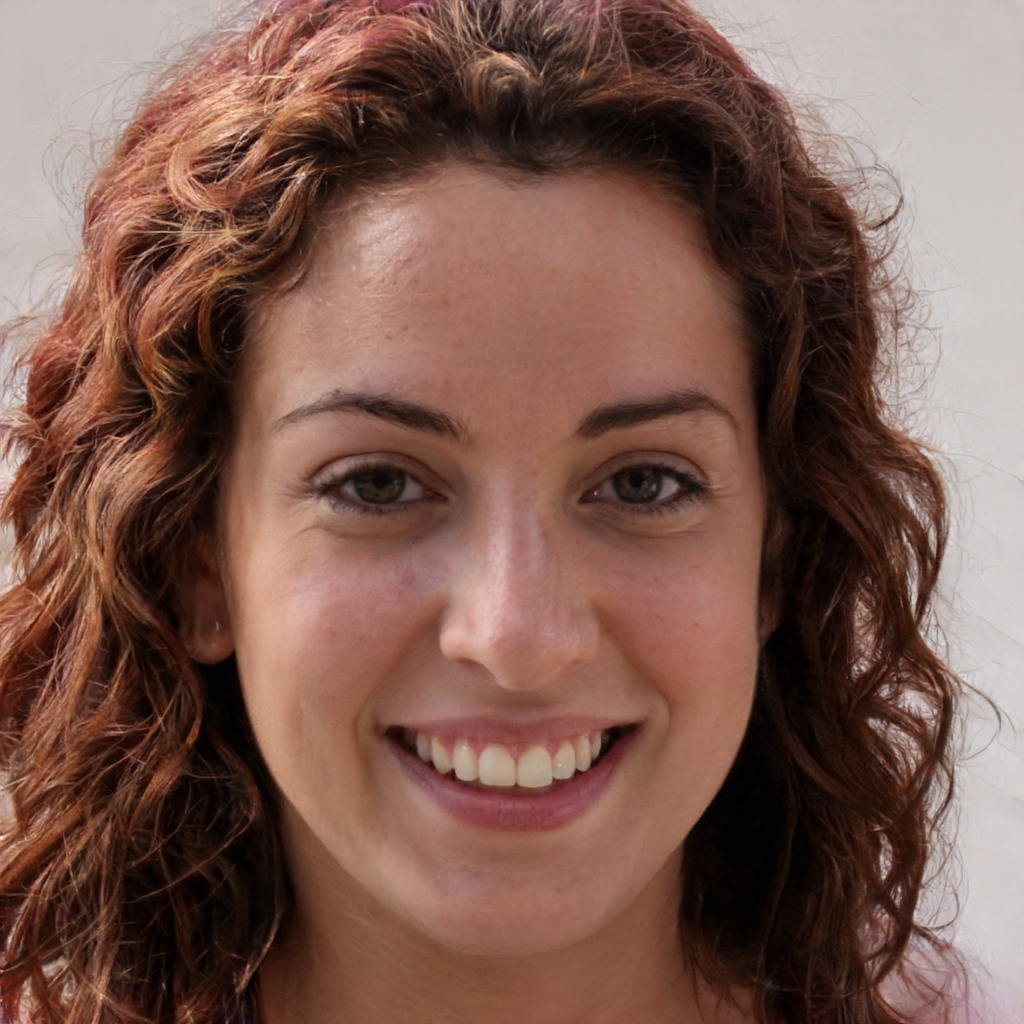
We came from a system that clearly surpassed us. Now we really spend very little time on follow-up. The notification mechanism allows us to rest assured that everything is going according to plan.